RWTH Aachen, Metallurgische Prozesstechnik und Metallrecycling
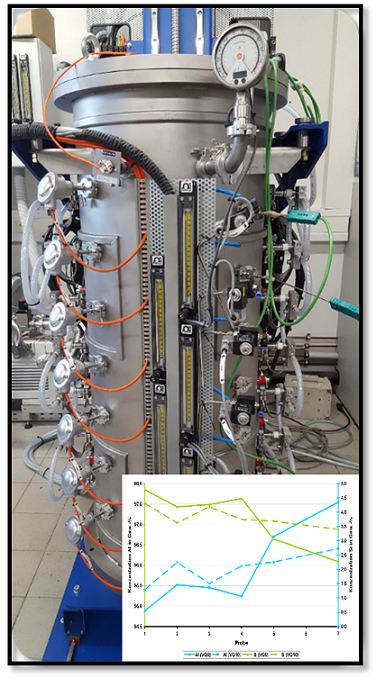
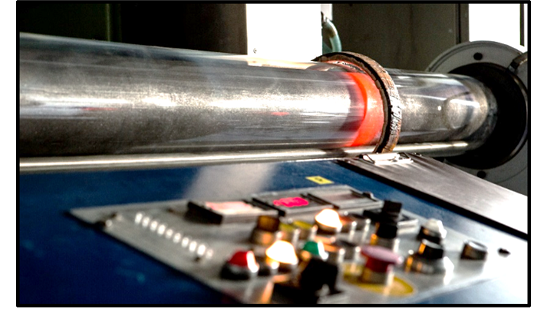
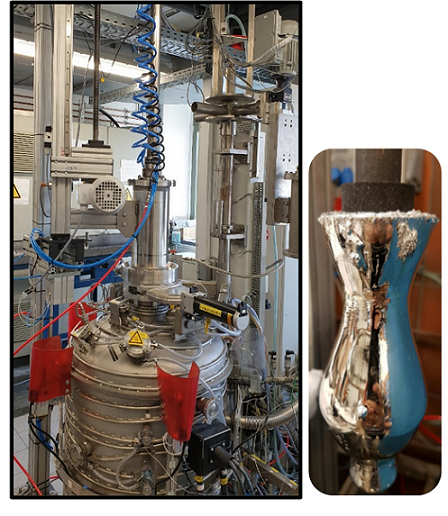
Das IME gehört europaweit zu den führenden Entwicklungszentren für umweltschonende Prozesse beim Metallrecycling. Zwischen 1996 und 2003 koordinierte es als Gründungsmitglied des SFB 525 "Ressourcenorientierte Gesamtbetrachtung von Stoffströmen metallischer Rohstoffe" Arbeiten der Metallrückgewinnung und -weiterverarbeitung. Seit dem Jahr 2000 wurden auf dem Gebiet "produktionsintegrierter Umweltschutz" zwölf europäische und national geförderte Forschungsgroßprojekte durchgeführt. Mit 1.000 m² Experimentalfläche lassen sich Prozessketten bis zum Demonstrationsmaßstab realisieren. Kernkompetenzen sind die Entwicklung nachhaltig umweltschonender und kosteneffizienter Verfahren zur Herstellung, Reinigung und zum Recycling metallischer Werkstoffe. Die Forschungsschwerpunkte des IME unterliegen zwangsläufig den sich stetig verändernden Bedürfnissen und Prioritäten der politischen Anforderungen wie auch die der verbundenen Industrieunternehmen. Nahezu die gesamte Bandbreite der Metalle wird hierbei abgedeckt, mit aktuellen Schwerpunkten auf Ti, Si, Ge, Sb, Al, Mg, Cu sowie den Seltenen Erden. Darüber hinaus beschäftigt sich das IME seit Jahren in Forschung und Lehre mit dem Thema „Entfernung metallischer Verunreinigungen aus Schmelzen“, insbesondere um extrem hohe Reinheitsgrade zu erzielen. Derzeit laufen im „Pure Metals Group“ des IMEs Arbeiten zur High-Purity-Raffination von Aluminium, Magnesium, Antimon sowie Germanium und Tellurium. In diesem Zusammenhang erforscht das IME in den letzten Jahren grundlegend drei Methoden zur Herstellung hochreiner Metalle. Ein statischer Kristallisationsofen, der in sieben Widerstandszonen eingeteilt ist, die einzeln über eine programmierbare Steuerung angesteuert und auf die gewünschte Temperatur gebracht werden können. So kann ein vorgegebenes Abkühlprofil automatisch abgefahren werden, wobei die Abkühlung nur durch eine Regulierung der eingebrachten Leistung geschieht und keine zusätzliche externe Kühlung verwendet wird. Die Verunreinigungen mit einem Verteilungskoeffizienten kleiner als eins sollen in der Rest-Schmelze, während die mit einem Verteilungskoeffizienten großer als eins am Boden des Tiegels angereichert werden, sodass nach späterer Entfernung des Bodens und des oberen Deckels ein raffinierter Block des Zielmetalls verbleibt (siehe Abb. 1).
Eine horizontale Zonenschmelze-Anlage (Abb. 2), gesteuert mittels einer induktiven Leistung von max. 45 kW, erlaubt eine Vorschubgeschwindigkeit von max. 1,99 mm/min und wurde bislang erfolgreich zur Reinigung von Aluminium von 3N auf 4N eingesetzt. Hier haben die Komplexität der Kontrolle des Reinheitsgrades durch die Länge der Schmelzzone sowie der hohe Zeitbedarf des Prozesses zur Idee der Erforschung der „Kühlfinger“-Methodik geführt. Die Arbeitsgruppe „Pure Metals“ am IME beschäftigt sich deshalb auch mit dem Thema Metallraffination mittels Kühlfinger (siehe Abb. 3). Die exakte Kontrolle des Temperaturgradienten, selbst beeinflusst u.a. durch die Rotation des Fingers sowie den Kühlgasdurchfluss, ist die wichtigste Herausforderung bei der Entwicklung dieser Methodik, denn diese Parameter haben einen direkten Effekt sowohl auf die Form der Kristallisation als auch auf die Wachstumsgeschwindigkeit des kristallisierten Materials und somit auf die Effizienz der Verunreinigungsentfernung.